Thermal Bridging and Condensation: Addressing the Hidden Issues in Modern Homes
Look at the photograph above. It was taken around 9am on a frosty winter morning in Christchurch. Look at the stark evidence of thermal bridging in the timber framed wall; note the warm spots where the traditional mid-floor is (above the ground floor windows), also the warmer areas at the top of the wall where the condensation has dried out. One way to look at it is; the heat from within the home is being used to warm up the cladding. In other words; it's being wasted.
The Problem
Thermal bridging and condensation are significant issues in residential construction that can lead to uncomfortable living conditions, higher energy bills, and long-term damage to the building structure. Understanding these problems is crucial for homeowners and builders aiming to create energy-efficient and healthy homes.
The Causes and Implications
Thermal Bridging occurs when materials that are poor insulators come into contact with the building envelope, creating a pathway for heat to escape. Common thermal bridges include metal window frames, wall studs, and other structural elements that interrupt the continuity of the insulation layer. These bridges allow heat to bypass the insulation, leading to increased energy loss and higher heating and cooling costs.
Here is another image of a home wall; this is on the south side of the building. The lighter patches are dry, because the warmth of the escaping heat has dried out the external condensation. The parts that have the condensation are in fact where the insulation has been fitted. This is a traditional timber framed home. The warmer spots show up where the framing is, and also, note how the warmer air is getting into the framing more at the top of the wall than at the bottom of the wall.
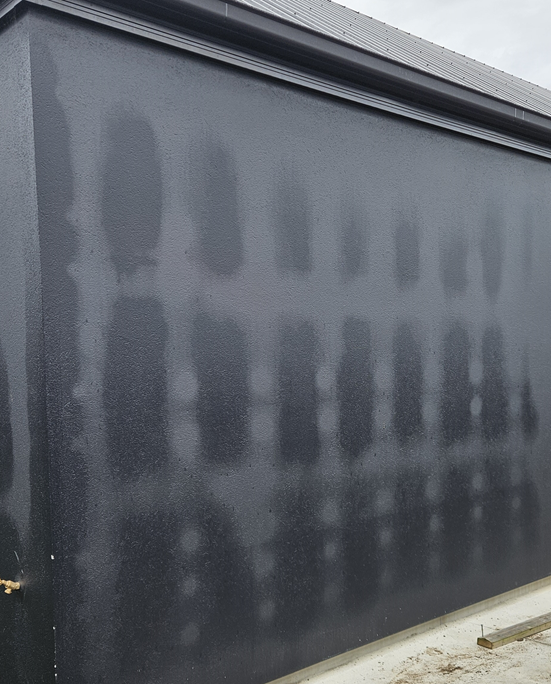
The implications of thermal bridging are multifaceted:
- Increased Energy Consumption: Thermal bridges can significantly reduce the overall R-value of the building envelope, leading to higher energy use to maintain comfortable indoor temperatures.
- Cold Spots: These areas can lead to discomfort for occupants and may also cause localized condensation issues.
- Condensation and Moisture Problems: When warm, moist air comes into contact with cold surfaces, condensation occurs. This can lead to mold growth, wood rot, and other moisture-related issues, which are detrimental to both the building structure and occupant health (Homepage).
Condensation is the result of moisture in the air turning into liquid when it comes into contact with cooler surfaces. This can happen inside walls, on windows, or in poorly ventilated areas. The presence of condensation is often a sign of inadequate thermal insulation and poor air sealing.
The Causes of Thermal Bridging and Condensation
Thermal bridging and condensation issues typically arise from:
- Poor Insulation Practices: Inadequate or improperly installed insulation leaves gaps that become pathways for heat transfer.
- Building Materials: Traditional building materials like metal and wood can create thermal bridges due to their conductive properties.
- Construction Techniques: Conventional framing methods often interrupt the insulation layer, creating points where heat can easily escape.
- Ventilation Issues: Insufficient ventilation can trap moisture inside the building, leading to condensation on cold surfaces (Homepage).
The Implications of Thermal Bridging and Condensation
The implications of thermal bridging and condensation are severe and multifaceted:
- Energy Inefficiency: Buildings with significant thermal bridging require more energy to heat and cool, leading to higher utility bills and increased environmental impact.
- Structural Damage: Persistent condensation can lead to mold growth, wood rot, and degradation of building materials, compromising the structural integrity of the home (Homepage).
- Health Concerns: Mold and mildew resulting from condensation can pose serious health risks to occupants, including respiratory issues and allergies.
- Comfort Issues: Cold spots created by thermal bridging can make indoor spaces uncomfortable, reducing the overall quality of living conditions.
Ways of Overcoming the Issues
- Continuous Insulation: Ensuring that the insulation layer is continuous and uninterrupted by structural elements can greatly reduce thermal bridging. Materials such as SIPs (Structural Insulated Panels) provide this continuous layer of insulation.
- Thermal Breaks: Incorporating thermal breaks in areas where structural elements penetrate the insulation layer can prevent thermal bridging. This involves using materials with low thermal conductivity to separate the thermal bridge from the building envelope.
- Proper Ventilation: Adequate ventilation helps control indoor humidity levels, reducing the risk of condensation. Mechanical ventilation systems can be particularly effective in maintaining consistent air quality and moisture levels.
- Air Sealing: Ensuring that the building envelope is airtight prevents warm, moist air from leaking into cooler areas where it can condense. This involves sealing gaps and cracks in the building structure.
- Advanced Framing Techniques: Techniques such as staggered stud walls or double-stud walls can minimize thermal bridging by reducing the number of direct conductive paths through the insulation layer.
- High-Performance Windows and Doors: Installing windows and doors with high thermal performance can reduce thermal bridging at these common weak points. Look for products with low U-values and thermal breaks within the frames.
Why Formance SIPs Are a Very Good Solution
Formance SIPs offer an excellent solution to the problems of thermal bridging and condensation:
- Continuous Insulation: Formance SIPs consist of an insulating foam core sandwiched between two structural facings, typically oriented strand board (OSB). This design provides a continuous layer of insulation with minimal thermal bridging, which significantly improves the thermal performance of the building envelope.
- Airtight Construction: SIPs are manufactured in large sections, which means there are fewer gaps and joints that need to be sealed compared to traditional framing. This results in a much tighter building envelope, reducing air leaks and improving energy efficiency.
- High R-Values: The insulation provided by SIPs is consistent and reliable, ensuring that the building's thermal performance matches its rated R-value. This is unlike traditional framing, where thermal bridging can significantly reduce the effective R-value of the walls.
- Speed and Efficiency: Building with SIPs is faster and more efficient than traditional methods. The panels are prefabricated and can be quickly assembled on-site, reducing labor costs and construction time. This efficiency does not compromise the quality of insulation or structural integrity, making SIPs an ideal choice for modern construction projects.
- Energy Savings: By reducing thermal bridging and improving insulation, Formance SIPs can lead to significant energy savings over the life of the building. This not only lowers utility bills but also contributes to a more sustainable and environmentally friendly home.
- Enhanced Comfort: The superior insulation and airtightness provided by Formance SIPs create a more stable and comfortable indoor environment. This reduces the occurrence of cold spots and drafts, enhancing the overall living experience for occupants.
- Moisture Control: Formance SIPs help to control moisture levels within the building by preventing condensation build-up. This reduces the risk of mold growth and structural damage, contributing to a healthier and more durable home (Homepage).
In conclusion, addressing thermal bridging and condensation is essential for creating comfortable, energy-efficient homes. Formance SIPs provide a comprehensive solution by offering continuous insulation, airtight construction, and high thermal performance, making them an excellent choice for modern residential construction. By integrating these advanced building techniques, homeowners and builders can achieve superior energy efficiency, enhanced comfort, and long-term durability in their homes.
References.
High-performance Construction Details Manual:
- This guide includes a comprehensive library of construction details specifically designed for high-performance buildings. This manual covers elements such as walls, roofs, junctions, slabs, and window installations, offering both 1-D and 2-D details with associated heat transfer calculations. The guide is a collaborative effort funded in part by the building research levy and includes contributions from BRANZ, PHINZ, Resilienz, MBIE, and Beacon Pathway.
For more information and to access the guide, you can visit the Sustainable Engineering Ltd website and the PHINZ website where the handbook is available for download and review.
BRANZ:
- BRANZ provides insights on thermal bridging leading to condensation issues, especially in poorly insulated homes. They emphasize the importance of addressing thermal bridging to maintain a healthy indoor environment. BRANZ Build
Building Performance (MBIE):
- The MBIE website outlines the Building Code requirements in New Zealand, focusing on insulation to limit condensation. It highlights the importance of thermal breaks, particularly for steel framing, to reduce condensation risks. Building Performance (MBIE)